What is the CNC?
- Share
- Issue Time
- Jul 1,2019
Summary
Numerical control (CNC) (also computer numerical control (CNC)) is the automated control of machining tools (drills, boring tools, lathes) and 3D printers by means of a computer.
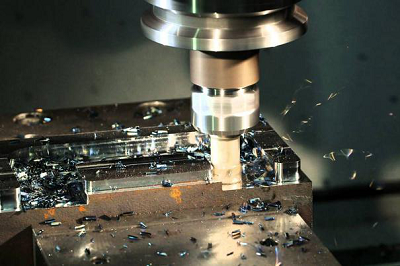
Numerical control (CNC) (also computer numerical control (CNC)) is the automated control of machining tools (drills, boring tools, lathes) and 3D printers by means of a computer. A CNC machine processes a piece of material (metal, plastic, wood, ceramic, or composite) to meet specifications by following a coded programmed instruction and without a manual operator.
A CNC machine is a motorized maneuverable tool and often a motorized maneuverable platform, which are both controlled by a computer core, according to specific input instructions. Instructions are delivered to a CNC machine in the form of graphical computer-aided design (CAD) files, which are transformed into a sequential program of machine control instructions such as G-code, and then executed. In the case of 3D Printers, the part to be printed is "sliced", before the instructions (or the program) is generated.
CNC is an advance machine, and is a vast improvement over non-computer type machining that requires manual control, by hand wheels or levers, or mechanical control by fabricated pattern guides (cams). In modern CNC systems, the design of a mechanical part and its manufacturing program is highly automated. The part's mechanical dimensions are defined using CAD software, and then translated into manufacturing directives by computer-aided manufacturing (CAM) software. The resulting directives are transformed (by "post processor" software) into the specific commands necessary for a particular machine to produce the component, and then are loaded into the CNC machine.
Since any particular component might require the use of a number of different tools – drills, saws, etc. – modern machines often combine multiple tools into a single "cell". In other installations, a number of different machines are used with an external controller and human or robotic operators that move the component from machine to machine. In either case, the series of steps needed to produce any part is highly automated and produces a part that closely matches the original CAD.
Description
Motion is controlling multiple axes, normally at least two (X and Y),[1] and a tool spindle that moves in the Z (depth). The position of the tool is driven by direct-drive stepper motors or servo motors in order to provide highly accurate movements, or in older designs, motors through a series of step-down gears. Open-loop control works as long as the forces are kept small enough and speeds are not too great. On commercial metalworking machines, closed loop controls are standard and required in order to provide the accuracy, speed, and repeatability demanded.
Parts Description
As the controller hardware evolved, the mills themselves also evolved. One change has been to enclose the entire mechanism in a large box as a safety measure, often with additional safety interlocks to ensure the operator is far enough from the working piece for safe operation. Most new CNC systems built today are 100% electronically controlled.
CNC-like systems are used for any process that can be described as movements and operations. These include laser cutting, welding, friction stir welding, ultrasonic welding, flame and plasma cutting, bending, spinning, hole-punching, pinning, gluing, fabric cutting, sewing, tape and fiber placement, routing, picking and placing, and sawing.
Examples of CNC machines
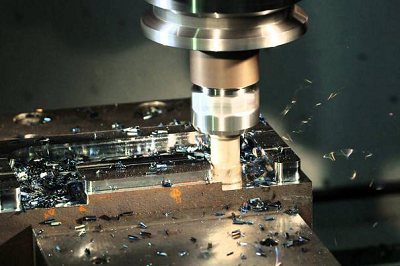
Mill
Translates programs consisting of specific numbers and letters to move the spindle (or workpiece) to various locations and depths. Many use G-code. Functions include: face milling, shoulder milling, tapping, drilling and some even offer turning. Today, CNC mills can have 3 to 6 axes. Most CNC mills require placing your workpiece on or in them and must be at least as big as your workpiece, but new 3-axis machines are being produced that you can put on your workpiece, and can be much smaller.
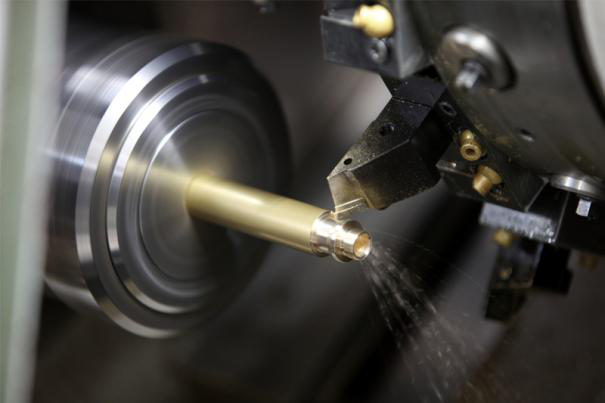
Lathe
Cuts workpieces while they are rotated. Makes fast, precision cuts, generally using indexable tools and drills. Effective for complicated programs designed to make parts that would be infeasible to make on manual lathes. Similar control specifications to CNC mills and can often read G-code. Generally have two axes (X and Z), but newer models have more axes, allowing for more advanced jobs to be machined.
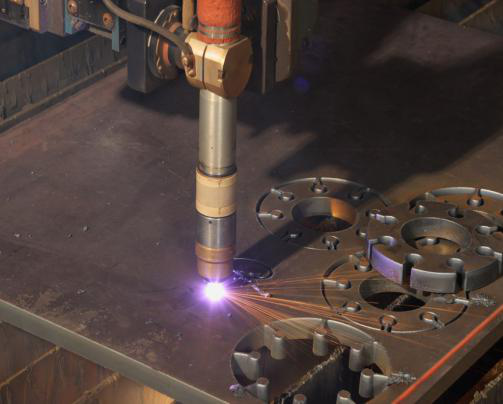
Plasma cutter
Involves cutting a material using a plasma torch. Commonly used to cut steel and other metals, but can be used on a variety of materials. In this process, gas (such as compressed air) is blown at high speed out of a nozzle; at the same time, an electrical arc is formed through that gas from the nozzle to the surface being cut, turning some of that gas to plasma. The plasma is sufficiently hot to melt the material being cut and moves sufficiently fast to blow molten metal away from the cut.
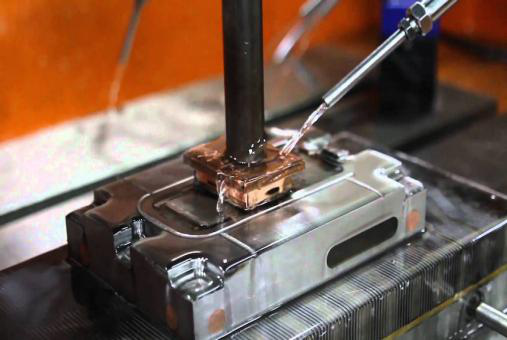
Electric discharge machining
(EDM), also known as spark machining, spark eroding, burning, die sinking, or wire erosion, is a manufacturing process in which a desired shape is obtained using electrical discharges (sparks). Material is removed from the workpiece by a series of rapidly recurring current discharges between two electrodes, separated by a dielectric fluid and subject to an electric voltage. One of the electrodes is called the tool electrode, or simply the "tool" or "electrode," while the other is called the workpiece electrode, or "workpiece."
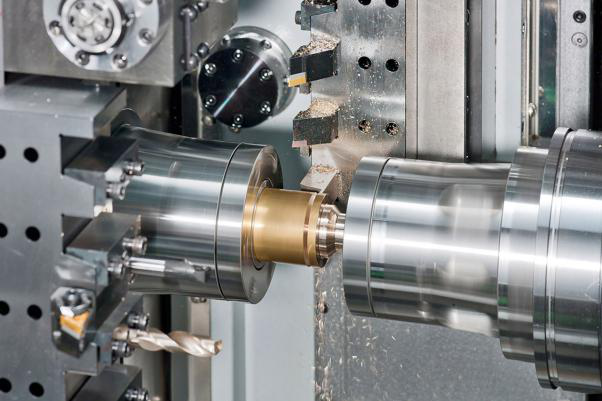
Multi spindle machine
Type of screw machine used in mass production. Considered to be highly efficient by increasing productivity through automation. Can efficiently cut materials into small pieces while simultaneously utilizing a diversified set of tooling. Multi-spindle machines have multiple spindles on a drum that rotates on a horizontal or vertical axis. The drum contains a drill head which consists of a number of spindles that are mounted on ball bearings and driven by gears. There are two types of attachments for these drill heads, fixed or adjustable, depending on whether the centre distance of the drilling spindle needs to be varied.
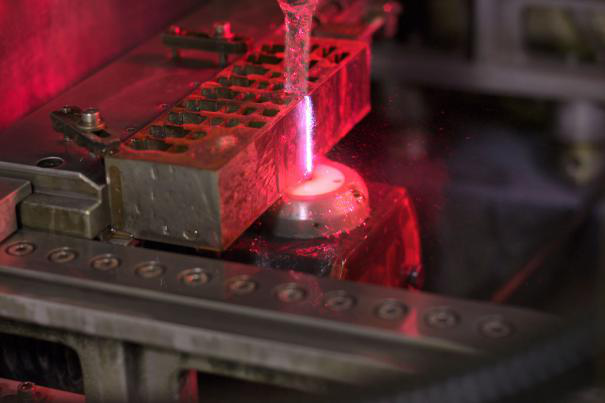
Wire EDM
Also known as wire cutting EDM, wire burning EDM, or traveling wire EDM, this process uses spark erosion to machine or remove material from any electrically conductive material, using a traveling wire electrode. The wire electrode usually consists of brass- or zinc-coated brass material. Wire EDM allows for near 90 degree corners and applies very little pressure on the material. Since the wire is eroded in this process, a wire EDM machine feeds fresh wire from a spool while chopping up the used wire and leaving it in a bin for recycling.
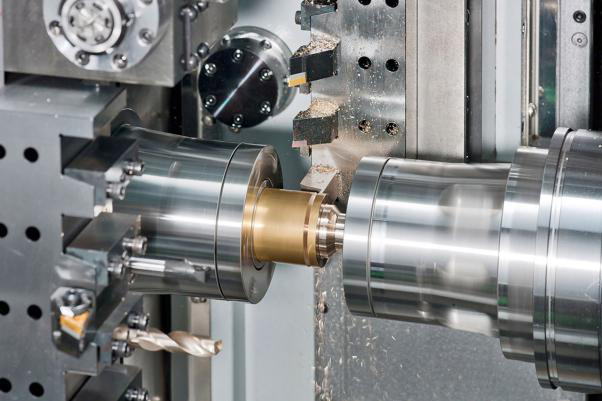
Sinker EDM
Also called cavity type EDM or volume EDM, a sinker EDM consists of an electrode and workpiece submerged in oil or another dielectric fluid. The electrode and workpiece are connected to a suitable power supply, which generates an electrical potential between the two parts. As the electrode approaches the workpiece, dielectric breakdown occurs in the fluid forming a plasma channel and small spark jumps. Production dies and moulds are often made with sinker EDM. Some materials, such as soft ferrite materials and epoxy-rich bonded magnetic materials are not compatible with sinker EDM as they are not electrically conductive.[6]
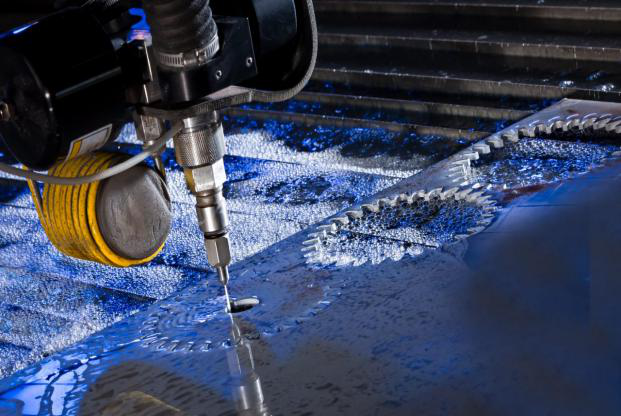
Water jet cutter
Also known as a "waterjet", is a tool capable of slicing into metal or other materials (such as granite) by using a jet of water at high velocity and pressure, or a mixture of water and an abrasive substance, such as sand. It is often used during fabrication or manufacture of parts for machinery and other devices. Waterjet is the preferred method when the materials being cut are sensitive to the high temperatures generated by other methods. It has found applications in a diverse number of industries from mining to aerospace where it is used for operations such as cutting, shaping, carving, and reaming.